

C2 bypasses R2,3 at signal frequencies so in an ideal world the input impedance would be 1M. I omitted D1 and D2, because they are there to protect against overload. We can test what happens either using Spice or what really happens by breadboarding it I’m a real world guy so I breadboarded it.įor laziness I used 27k instead of 56k for R2, R3 and 47u all round because this came to hand. The circuit is pitched at a noninverting gain of 11. Let’s take a look at the datasheet on where on page 5 Table 7.5 they cite an open loop input resistance ri of min 30k typ 100k. I disagree with the hypothesis that the open-loop input resistance (you indicate 300k, TI seems to indicate 100k) determines the input resistance of this circuit, because of the action of negative feedback. Only then did I look at what was going on.
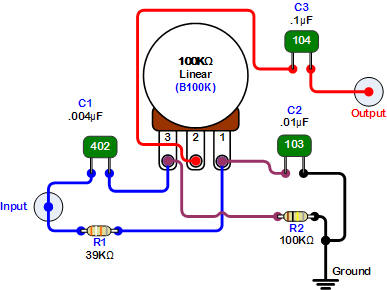

I have to admit that I made the same assumption initially and used a TL071, but it proved surprisingly noisy in this application, and since I’d socketed the opamp to be able to reuse it, I tried a NE5534 and was rewarded with lower noise. A more practical stereo version of this was constructed in a box, measurements and test results are available. This goes to show that the piezo contact mic, for all its uneven frequency response faults, is capable of an excellent noise performance when used correctly. NE5534 at same gain as test circuit but with the contact mic replacing the 1k tone. However, the piezo mic has not raised the noise level significantly. You wouldn’t normally have to put up with this level of hum – building the circuit into a metal box and using screened cable to the piezo device would fix that. About 3/4 of the way in some piece of machinery is started by my neighbours – I did not hear this at the time but it was conducted through the house into the shelf with the mic. The hum is because this circuit is on a breadboard with the mic laid on the shelf, and some of the hum is mechanical, from the transformer of the power supply powering the unit, which is on the same shelf unit. At the back of my mind was the wonder whether a piezo mic would not have more self-noise anyway, so I removed the test tone and put in the mic. Matching levels of the 1kHz test tone to correct for the slight difference in gain shows the NE5534 offers a noise floor 10-20dB lower than the 2N3819, in return for extra complexity. At the start of the recording you can faintly hear woodpigeons calling above the surface propagating through the water, and aircraft noise, before the chomping sound Rightmark display of the noise difference between the left (2N3819) and right (NE5534) versions Noise comparison of 2n3819 single fet with opamp version using a NE5534 (left and right channels respectively) įreshwater hydrophone recording using this with an air cell piezo disk hydrophone.
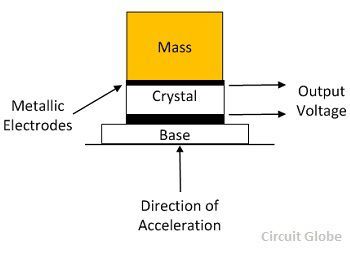
However, substituting the TL071 for the usual audio workhorse opamp, the bipolar NE5534 brought the lowest noise of all. a 7mV rms 1kHz signal was fed into a 10k:12ohm attenuator, and then coupled via a 15nF capacitor to approximate the piezo source, generating 8uV. You can leave C1 and R4 out if you need less gain, though there is much to be said for the cheap version if you have lots of signal. FET Mic amplifier – opamp versionĭiodes D1,D2 stop you destroying the opamp with large signals from the piezo device if you drop it. The first thing that sprang to mind was a TL071 – the overall schematic is shown below. The calculation in the introduction showed a load of 330k was enough, so 1 meg is plenty for a contact mic. Although they are high impedance, they don’t need an outrageously high load impedance – not like an electret mic, where you need gigaohms to avoid losing bass. Piezo mics aren’t usually considered hi-fi, so distortion isn’t usually a problem of the amplifier – at high levels the mic will not be particularly linear. This is the purist approach solution to the tinny contact mic sound problem if you want the lowest electrical noise, or the lowest distortion at higher levels.
